Taizhou Fupusi Machinery Co., Ltd.
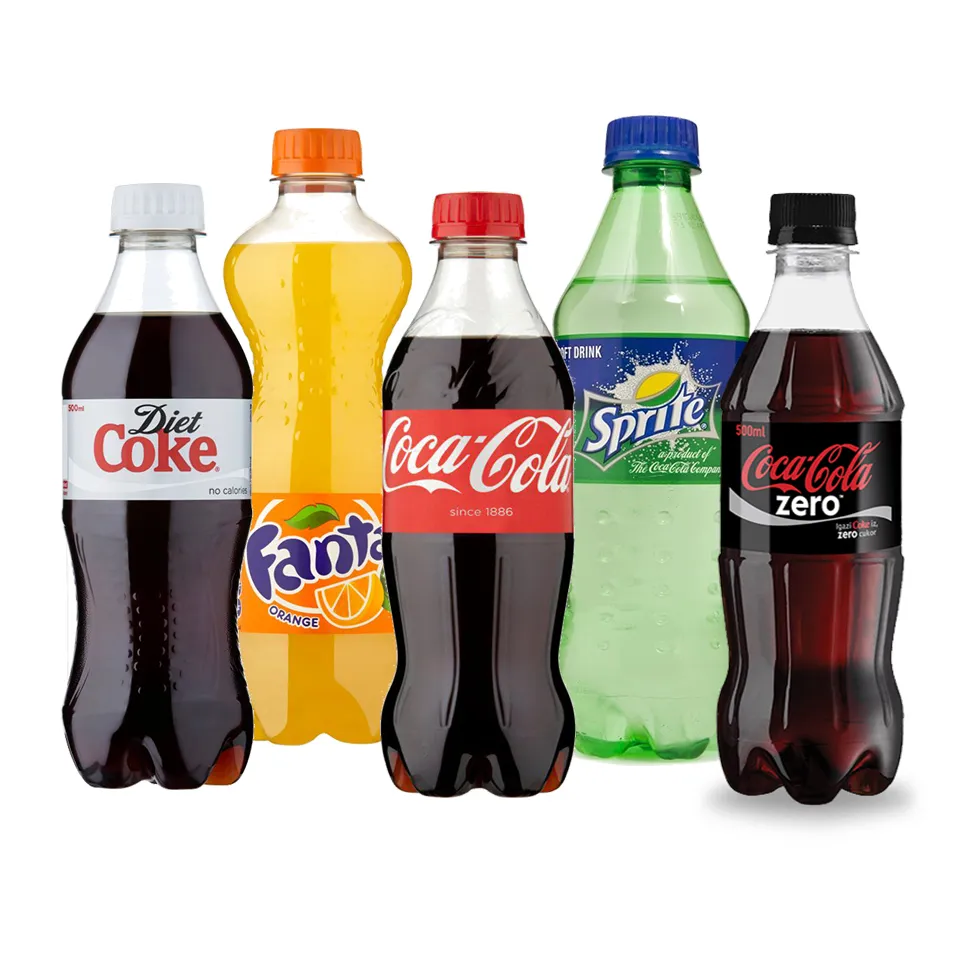
4. Reasons and solutions for general quality problems of heat-resistant PET bottles in the production process
Bottleneck skew
1. The oil passage is blocked, clear the oil passage of the mold body
2. Exhaust hole of the stretch rod is blocked. Clear the blowing hole of the stretch rod
3. The nozzle seal is damaged. Replace the nozzle seal
Center point deviation
1. Pre-blowing pressure is too high, reduce pre-blowing pressure
2. The pre-blowing flow is too large, reduce the pre-blowing flow
3. Pre-blowing position is too early, postpone pre-blowing position
4. The stretch rod is bent Replace the stretch rod
5. The gap between the stretch rod and the bottom mold is too large. Adjust the gap between the stretch rods
6. The preform temperature is too high, reduce the preform setting temperature
The bottom of the bottle is deformed
1. The bottom mold oil temperature is too high, reduce the hot oil engine oil temperature
2. The bottom mold blow valve is damaged. Replace the bottom mold blow valve
3. The bottom temperature of the preform is too high, reduce the bottom temperature of the preform
Folds at the bottom of the bottle
1. The pre-blowing pressure is too small. Increase the pre-blowing pressure
2. The pre-blowing flow is too small. Increase the pre-blowing flow
3. Pre-blowing is too late, pre-blowing early
Stiff neck
1. Insufficient neck heating Increase the amount of neck heating
2. The pre-blowing pressure is too large, reduce the pre-blowing pressure
3. The pre-blowing flow is too large, reduce the pre-blowing flow
4. Pre-blowing too early, delay pre-blowing
5. The position of the heating furnace is too high. Adjust the position of the heating furnace
6. The stretching rod is slow. Overhaul the stretching cylinder
Poor forming of parting line
1. The mold compensation seal is damaged. Replace the compensation seal
2. Improper adjustment of the mold gap Adjust the mold gap
Wall deformation before irrigation
1. The cooling blow time is too short. Extend the cooling blow time
2. The mold body temperature is too high, reduce the mold body temperature
3. There is no cooling air blowing out of the stretch rod. Overhaul the stretch rod blowing system
Wall deformation after irrigation
1. The mold body temperature is too low to increase the temperature of the mold body hot oil
2. The set temperature of the preform is too low. Increase the set temperature of the preform
3. The cooling blow time is too long, reduce the cooling blow time
4. Uneven distribution of plastics Adjust the blowing process to make the distribution of materials even
5. The flow of hot oil is too small, clear the oil circuit and clean the oil filter
Large shrinkage
1. Low mold temperature Increase mold temperature
2. The preform temperature is low, increase the preform setting temperature
3. The cooling blow time is too long, shorten the cooling blow time
4. The oil passage is blocked, clear the oil passage
The diameter is too large or too small
1. Improper setting of cooling blow time Adjust the cooling blow time
2. Uneven distribution of plastics Adjust the process to make the distribution of materials even
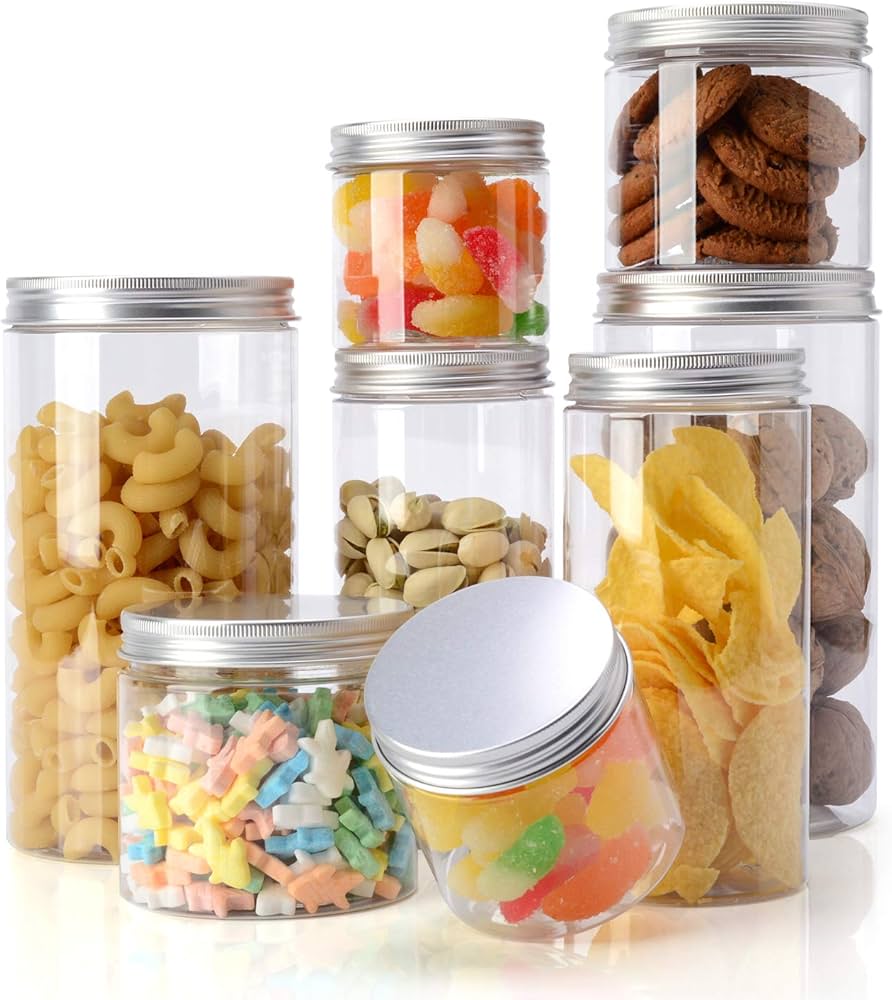
5. Common problems and solutions in the use of PET bottles in hot filling lines
1. Storage and transportation conditions and the storage period of the bottle.
Due to the hygroscopic properties of PET, placing PET (including slices, preforms and bottles) in the air will absorb moisture in the air. The longer it is placed, the more water it will absorb. The moisture content in PET will directly affect its performance. For hot-filled bottles, it will affect the heat-resistant temperature of hot-filled bottles. The more water content, the lower the heat-resistant temperature of the bottle. Generally speaking, for hot-filled bottles, during the period from the production of the preform to the filling of the beverage, the recommended placement time:
Bottle storage period: >1L within two weeks, <1L within three weeks; but recently, more and more manufacturers use lightweight bottles and connected production, that is, blow and fill, and the bottle storage period is within 6 hours. Blow-and-fill bottles can be filled with hot liquid at 95°C. Bottles stored for more than 24 hours after blowing can only be filled with hot liquid at 88°C.
Bottle materials and storage conditions (room temperature, relative humidity, length of storage time) will affect the technical indicators of hot-filled bottles, that is: the production of bottles should be based on the above different materials, storage conditions, customer requirements, etc., accordingly Adjust the blowing process and technical parameters. PET will undergo a hydrolysis reaction when it is melted and plasticized under normal humidity. High humidity content often leads to immediate reaction, resulting in molecular chain breaking, degradation, and molecular weight reduction (that is, lower IV). The mechanical properties of PET are related to the intrinsic viscosity IV. The lower the IV, the worse the mechanical properties of PET.
The annual average relative humidity in Jiangnan and coastal areas is 85%. In some areas, the relative humidity can be as high as 90% in spring and summer. In a high humidity environment, PET will absorb moisture and reach the maximum saturation humidity.
The higher the moisture content, the greater the drop in the IV value of PET. When the water content of a certain type of PET is 0.01%, its intrinsic viscosity is 0.73, and when the water content is 0.02%, its intrinsic viscosity becomes 0.63. At 180°C, the intrinsic viscosity decreases by 0.10 due to the reduction of the drying time by 3/4 hour.
The longer the drying time, the lower the moisture in the PET raw material, but excessive drying can also cause PET degradation. When heated to 180°C, for raw materials with a maximum initial moisture content of 0.3%, the moisture drops to 0.14%; drying for 4 hours can obtain a moisture content of 0.004%, which is the upper limit for controlling the moisture content of the preform. The moisture in the molecules of the bottle mouth will accelerate the crystallization of PET, and the moisture in the molecules of the bottle body will affect the arrangement of molecular chains.